VisitBasis has been providing software for merchandising automation in store for several years and one of the issues we hear the most from our customers is that they want to implement a system for minimizing out-of-stocks at retail stores.
We completely understand this. Out-of-stock means more than no sale: It could mean that customers are forever lost to a competing brand or store and has the potential of, little by little, eroding revenues.
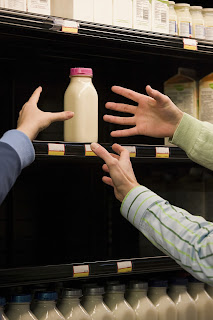
Minimizing out-of-stocks with VisitBasis software for automation in store is easy. However, it takes a couple of extra steps on the Office App in order to streamline audits and get reports that are easy to ready and therefore easy to act on.
Here is an outline of what needs to be configured in order to build an effective system to minimize out-of-stocks with VisitBasis:
1.Configure store must-stock lists (MSL)
On VisitBasis you can configure location MSL/ planograms individually or for a group of stores. This allows tasks to apply only to the products that are available at each store, remove the “noise” from products that should not be displayed, and speed up task completion.
2. Pre-select out-of-stock task for reps
One of the main issues in software for merchandising automation in store, especially when reps set up their own visit schedule, is that they also have to select their activities. By pre-selecting the out-of-stock task for all stores, reps will be “forced” to complete the task before closing visits and therefore report on out-of-stocks every time they visit a store, increasing management oversight.
3.Create meaningful tasks
An out-of-stock task template does not have to be complex. It can consist of only one question: “Out of stock?”, with the answer options “yes” or “no”. This also helps management filter reports in order to, over time, detect patterns and adjust shipment size and frequency, minimizing out-of-stocks.
Want to see more capabilities of VisitBasis software for merchandising automation?